CNC數控切削中十二個經驗總結!
2020-04-09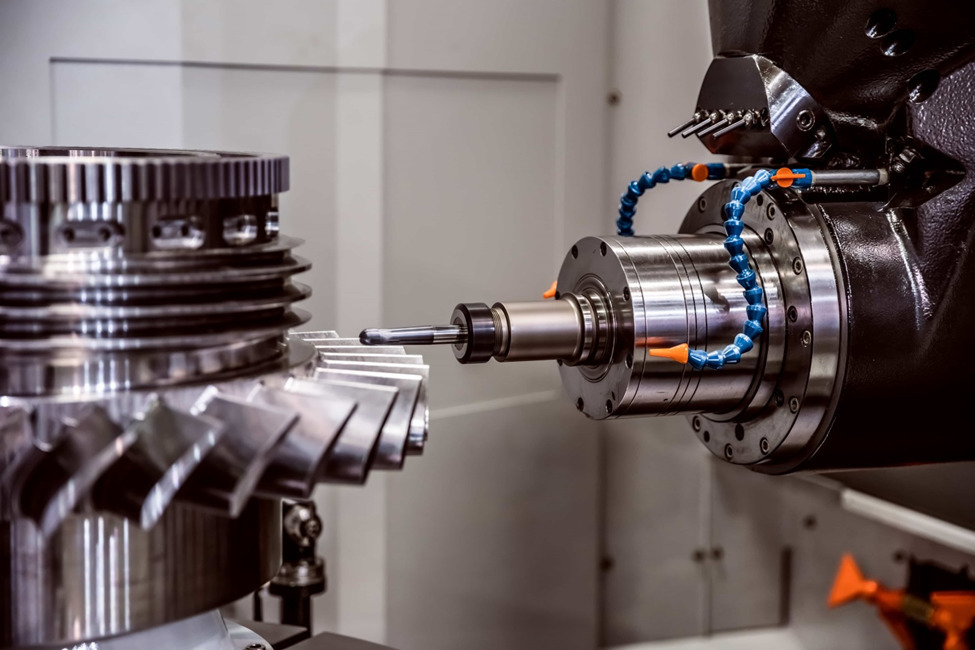
由於數控切削的複雜性(如不同的工具機,不同的材料,不同的鎢鋼銑刀,不同的切削方式,不同的參數設定等等),決定了從從事數控切削(無論是切削還是編程)到達一定水平,必須經過一段比較長的時間,以下是工程師在長期實際生產過程中總結出來的、有關數控切削工藝、工序、常用鎢鋼銑刀參數的選擇、切削過程中的監控等方面的一些經驗總匯,可供大家參考。
數控切削工序的劃分一般可按下列方法進行:
1、鎢鋼銑刀集中分序法就是按所用鎢鋼銑刀劃分工序,用同一把鎢鋼銑刀切削完零件上所有可以完成的部位。在用第二把刀、第三把完成它們可以完成的其它部位。這樣可減少換刀次數,壓縮空程時間,減少不必要的定位誤差。
2、以切削部位分序法對於切削內容很多的零件,可按其結構特點將切削部分分成幾個部分,如內形、外形、曲面或平面等。一般先切削平面、定位面,後切削孔;先切削簡單的幾何形狀,再切削複雜的幾何形狀;先切削精度較低的部位,再切削精度要求較高的部位。
3、以粗、精切削分序法對於易發生切削變形的零件,由於粗切削後可能發生的變形而需要進行校形,故一般來說凡要進行粗、精切削的都要將工序分開。綜上所述,在劃分工序時,一定要視零件的結構與工藝性,工具機的功能,零件數控切削內容的多少,安裝次數及本單位生產組織狀況靈活掌握。另建議採用工序集中的原則還是採用工序分散的原則,要根據實際情況來確定,但一定力求合理。
切削順序的安排應根據零件的結構和毛坯狀況,以及定位夾緊的需要來考慮,重點是工件的剛性不被破壞。順序一般應按下列原則進行:
1、上道工序的切削不能影響下道工序的定位與夾緊,中間穿插有通用工具機切削工序的也要綜合考慮。
2、先進行內形內腔切削序,後進行外形切削工序。
3、以相同定位、夾緊方式或同一把刀切削的工序最好連接進行,以減少重複定位次數,換刀次數與挪動壓板次數。
4、在同一次安裝中進行的多道工序,應先安排對工件剛性破壞小的工序。
在確定定位基準與夾緊方案時應注意下列三點:
1、力求設計、工藝、與編程計算的基準統一。
2、儘量減少裝夾次數,儘可能做到在一次定位後就能切削出全部待切削表面。
3、避免採用占機人工調整方案。
4、夾具要開暢,其定位、夾緊機構不能影響切削中的走刀(如產生碰撞),碰到此類情況時,可採用用虎鉗或加底板抽螺絲的方式裝夾。
1、對刀點可以設在被切削零件的上,但注意對刀點必須是基準位或已精切削過的部位,有時在第一道工序後對刀點被切削毀壞,會導致第二道工序和之後的對刀點無從查找,因此在第一道工序對刀時注意要在與定位基準有相對固定尺寸關係的地方設立一個相對對刀位置,這樣可以根據它們之間的相對位置關係找回原對刀點。這個相對對對刀位置通常設在工具機工作檯或夾具上。其選擇原則如下:
1)找正容易。
2)編程方便。
3)對刀誤差小。
4)切削時檢查方便、可查。
2、工件坐標系的原點位置是由操作者自己設定的,它在工件裝夾完畢後,通過對刀確定,它反映的是工件與工具機零點之間的距離位置關係。工件坐標系一旦固定,一般不作改變。工件坐標系與編程坐標系兩者必須統一,即在切削時,工件坐標系和編程坐標系是一致的。
走刀路線是指數控切削過程中鎢鋼銑刀相對於被切削件的運動軌跡和方向。切削路線的合理選擇是非常重要的,因為它與零件的切削精度和表面質量密卻相關。在確定走刀路線是主要考慮下列幾點:
1、保證零件的切削精度要求。
2、方便數值計算,減少編程工作量。
3、尋求最短切削路線,減少空刀時間以提高切削效率。
4、儘量減少程序段數。
5、保證工件輪廓表面切削後的粗糙度的要求,最終輪廓應安排最後一走刀連續切削出來。
6、鎢鋼銑刀的進退刀(切入與切出)路線也要認真考慮,以儘量減少在輪廓處停刀(切削力突然變化造成彈性變形)而留下刀痕,也要避免在輪廓面上垂直下刀而劃傷工件。
工件在找正及程序調試完成之後,就可進入自動切削階段。在自動切削過程中,操作者要對切削的過程進行監控,防止出現非正常切削造成工件質量問題及其它事故。
對切削過程進行監控主要考慮以下幾個方面:
1、切削過程監控粗切削主要考慮的是工件表面的多餘餘量的快速切除。在工具機自動切削過程中,根據設定的切削用量,鎢鋼銑刀按預定的切削軌跡自動切削。此時操作者應注意通過切削負荷表觀察自動切削過程中的切削負荷變化情況,根據鎢鋼銑刀的承受力狀況,調整切削用量,發揮工具機的最大效率。
2、切削過程中切削聲音的監控在自動切削過程中,一般開始切削時,鎢鋼銑刀切削工件的聲音是穩定的、連續的、輕快的,此時工具機的運動是平穩的。隨著切削過程的進行,當工件上有硬質點或鎢鋼銑刀磨損或鎢鋼銑刀送夾等原因後,切削過程出現不穩定,不穩定的表現是切削聲音發生變化,鎢鋼銑刀與工件之間會出現相互撞擊聲,工具機會出現震動。此時應及時調整切削用量及切削條件,當調整效果不明顯時,應暫停工具機,檢查鎢鋼銑刀及工件狀況。
3、精切削過程監控精切削,主要是保證工件的切削尺寸和切削表面質量,切削速度較高,進給量較大。此時應著重注意積屑瘤對切削表面的影響,對於型腔切削,還應注意拐角處切削過切與讓刀。對於上述問題的解決,一是要注意調整切削液的噴淋位置,讓切削表面時刻處於冷卻條件;二是要注意觀察工件的已切削面質量,通過調整切削用量,儘可能避免質量的變化。如調整仍無明顯效果,則應停機檢察原程序編得是否合理。
特別注意的是,在暫停檢查或停機檢查時,要注意鎢鋼銑刀的位置。如鎢鋼銑刀在切削過程中停機,突然的主軸停轉,會使工件表面產生刀痕。一般應在鎢鋼銑刀離開切削狀態時,考慮停機。
4、鎢鋼銑刀監控鎢鋼銑刀的質量很大程度決定了工件的切削質量。在自動切削切削過程中,要通過聲音監控、切削時間控制、切削過程中暫停檢查、工件表面分析等方法判斷鎢鋼銑刀的正常磨損狀況及非正常破損狀況。要根據切削要求,對鎢鋼銑刀及時處理,防止發生由鎢鋼銑刀未及時處理而產生的切削質量問題。
1、平面銑削時應選用不重磨硬質合金端銑刀或立銑刀。一般銑削時,儘量採用二次走刀切削,第一次走刀最好用端銑刀粗銑,沿工件表面連續走刀。每次走刀寬度推薦至為鎢鋼銑刀直徑的60%--75%。
2、立銑刀和鑲硬質合金刀片的端銑刀主要用於切削凸台、凹槽和箱口面。
3、球刀、圓刀(亦稱圓鼻刀)常用於切削曲面和變斜角輪廓外形。而球刀多用於半精切削和精切削。鑲硬質合金鎢鋼銑刀的圓刀多用於開粗。
1、切削程序單是數控切削工藝設計的內容之一,也是需要操作者遵守、執行的規程,是切削程序的具體說明,目的是讓操作者明確程序的內容、裝夾和定位方式、各個切削程序所選用的鎢鋼銑刀既應注意的問題等。
2、在切削程序單里,應包括:繪圖和編程文件名,工件名稱,裝夾草圖,程序名,每個程序所使用的鎢鋼銑刀、切削的最大深度,切削性質(如粗切削還是精切削),理論切削時間等。
在確定切削工藝後,編程前要了解:
1、工件裝夾方式;
2、工件毛胚的大小----以便確定切削的範圍或是否需要多次裝夾;
3、工件的材料----以便選擇切削所使用何種鎢鋼銑刀;
4、庫存的鎢鋼銑刀有哪些----避免在切削時因無此鎢鋼銑刀要修改程序,若一定要用到此鎢鋼銑刀,則可以提前準備。
安全高度的設定原則:一般高過島嶼的最高面。或者將編程零點設在最高面,這樣也可以最大限度避免撞刀的危險。
因為不同的工具機所能認到的地址碼和NC程序格式不同,所以要針對所使用的工具機選擇正確的後處理格式才能保證編出來的程序可以運行。
程序輸送的方式可分為CNC和DNC兩種,CNC是指程序通過媒體介質(如軟盤,讀帶機,通訊線等)輸送到工具機的存儲器存儲起來,切削時從存儲器里調出程序來進行切削。由於存儲器的容量受大小的限制,所以當程序大的時候可採用DNC方式進行切削,由於DNC切削時工具機直接從控制電腦讀取程序(也即是邊送邊做),所以不受存儲器的容量受大小的限制。
1、切削用量有三大要素:切削深度,主軸轉速和進給速度.切削用量的選擇總體原則是:少切削,快進給(即切削深度小,進給速度快)。
2、按材料分類,鎢鋼銑刀一般分為普通硬質白鋼刀(材料為高速鋼),塗層鎢鋼銑刀(如鍍鈦等),合金鎢鋼銑刀(如鎢鋼,氮化硼鎢鋼銑刀等)。
一、如何對切削工序進行劃分?
數控切削工序的劃分一般可按下列方法進行:1、鎢鋼銑刀集中分序法就是按所用鎢鋼銑刀劃分工序,用同一把鎢鋼銑刀切削完零件上所有可以完成的部位。在用第二把刀、第三把完成它們可以完成的其它部位。這樣可減少換刀次數,壓縮空程時間,減少不必要的定位誤差。
2、以切削部位分序法對於切削內容很多的零件,可按其結構特點將切削部分分成幾個部分,如內形、外形、曲面或平面等。一般先切削平面、定位面,後切削孔;先切削簡單的幾何形狀,再切削複雜的幾何形狀;先切削精度較低的部位,再切削精度要求較高的部位。
3、以粗、精切削分序法對於易發生切削變形的零件,由於粗切削後可能發生的變形而需要進行校形,故一般來說凡要進行粗、精切削的都要將工序分開。綜上所述,在劃分工序時,一定要視零件的結構與工藝性,工具機的功能,零件數控切削內容的多少,安裝次數及本單位生產組織狀況靈活掌握。另建議採用工序集中的原則還是採用工序分散的原則,要根據實際情況來確定,但一定力求合理。
二、切削順序的安排應遵循什麼原則?
切削順序的安排應根據零件的結構和毛坯狀況,以及定位夾緊的需要來考慮,重點是工件的剛性不被破壞。順序一般應按下列原則進行:1、上道工序的切削不能影響下道工序的定位與夾緊,中間穿插有通用工具機切削工序的也要綜合考慮。
2、先進行內形內腔切削序,後進行外形切削工序。
3、以相同定位、夾緊方式或同一把刀切削的工序最好連接進行,以減少重複定位次數,換刀次數與挪動壓板次數。
4、在同一次安裝中進行的多道工序,應先安排對工件剛性破壞小的工序。
三、工件裝夾方式的確定應注意那幾方面?
在確定定位基準與夾緊方案時應注意下列三點:1、力求設計、工藝、與編程計算的基準統一。
2、儘量減少裝夾次數,儘可能做到在一次定位後就能切削出全部待切削表面。
3、避免採用占機人工調整方案。
4、夾具要開暢,其定位、夾緊機構不能影響切削中的走刀(如產生碰撞),碰到此類情況時,可採用用虎鉗或加底板抽螺絲的方式裝夾。
四、如何確定對刀點比較合理?工件坐標系與編程坐標系有什麼關係?
1、對刀點可以設在被切削零件的上,但注意對刀點必須是基準位或已精切削過的部位,有時在第一道工序後對刀點被切削毀壞,會導致第二道工序和之後的對刀點無從查找,因此在第一道工序對刀時注意要在與定位基準有相對固定尺寸關係的地方設立一個相對對刀位置,這樣可以根據它們之間的相對位置關係找回原對刀點。這個相對對對刀位置通常設在工具機工作檯或夾具上。其選擇原則如下:1)找正容易。
2)編程方便。
3)對刀誤差小。
4)切削時檢查方便、可查。
2、工件坐標系的原點位置是由操作者自己設定的,它在工件裝夾完畢後,通過對刀確定,它反映的是工件與工具機零點之間的距離位置關係。工件坐標系一旦固定,一般不作改變。工件坐標系與編程坐標系兩者必須統一,即在切削時,工件坐標系和編程坐標系是一致的。
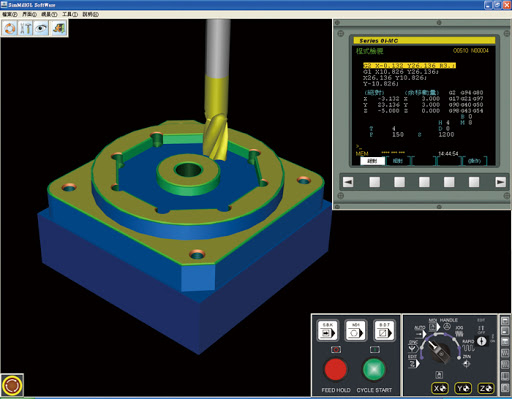
五、如何選擇走刀路線?
走刀路線是指數控切削過程中鎢鋼銑刀相對於被切削件的運動軌跡和方向。切削路線的合理選擇是非常重要的,因為它與零件的切削精度和表面質量密卻相關。在確定走刀路線是主要考慮下列幾點:1、保證零件的切削精度要求。
2、方便數值計算,減少編程工作量。
3、尋求最短切削路線,減少空刀時間以提高切削效率。
4、儘量減少程序段數。
5、保證工件輪廓表面切削後的粗糙度的要求,最終輪廓應安排最後一走刀連續切削出來。
6、鎢鋼銑刀的進退刀(切入與切出)路線也要認真考慮,以儘量減少在輪廓處停刀(切削力突然變化造成彈性變形)而留下刀痕,也要避免在輪廓面上垂直下刀而劃傷工件。
六、如何在切削過程中監控與調整?
工件在找正及程序調試完成之後,就可進入自動切削階段。在自動切削過程中,操作者要對切削的過程進行監控,防止出現非正常切削造成工件質量問題及其它事故。對切削過程進行監控主要考慮以下幾個方面:
1、切削過程監控粗切削主要考慮的是工件表面的多餘餘量的快速切除。在工具機自動切削過程中,根據設定的切削用量,鎢鋼銑刀按預定的切削軌跡自動切削。此時操作者應注意通過切削負荷表觀察自動切削過程中的切削負荷變化情況,根據鎢鋼銑刀的承受力狀況,調整切削用量,發揮工具機的最大效率。
2、切削過程中切削聲音的監控在自動切削過程中,一般開始切削時,鎢鋼銑刀切削工件的聲音是穩定的、連續的、輕快的,此時工具機的運動是平穩的。隨著切削過程的進行,當工件上有硬質點或鎢鋼銑刀磨損或鎢鋼銑刀送夾等原因後,切削過程出現不穩定,不穩定的表現是切削聲音發生變化,鎢鋼銑刀與工件之間會出現相互撞擊聲,工具機會出現震動。此時應及時調整切削用量及切削條件,當調整效果不明顯時,應暫停工具機,檢查鎢鋼銑刀及工件狀況。
3、精切削過程監控精切削,主要是保證工件的切削尺寸和切削表面質量,切削速度較高,進給量較大。此時應著重注意積屑瘤對切削表面的影響,對於型腔切削,還應注意拐角處切削過切與讓刀。對於上述問題的解決,一是要注意調整切削液的噴淋位置,讓切削表面時刻處於冷卻條件;二是要注意觀察工件的已切削面質量,通過調整切削用量,儘可能避免質量的變化。如調整仍無明顯效果,則應停機檢察原程序編得是否合理。
特別注意的是,在暫停檢查或停機檢查時,要注意鎢鋼銑刀的位置。如鎢鋼銑刀在切削過程中停機,突然的主軸停轉,會使工件表面產生刀痕。一般應在鎢鋼銑刀離開切削狀態時,考慮停機。
4、鎢鋼銑刀監控鎢鋼銑刀的質量很大程度決定了工件的切削質量。在自動切削切削過程中,要通過聲音監控、切削時間控制、切削過程中暫停檢查、工件表面分析等方法判斷鎢鋼銑刀的正常磨損狀況及非正常破損狀況。要根據切削要求,對鎢鋼銑刀及時處理,防止發生由鎢鋼銑刀未及時處理而產生的切削質量問題。
七、如何合理選擇切削鎢鋼銑刀?切削用量有幾大要素?有幾種材料的鎢鋼銑刀?如何確定鎢鋼銑刀的轉速,切削速度,切削寬度?
1、平面銑削時應選用不重磨硬質合金端銑刀或立銑刀。一般銑削時,儘量採用二次走刀切削,第一次走刀最好用端銑刀粗銑,沿工件表面連續走刀。每次走刀寬度推薦至為鎢鋼銑刀直徑的60%--75%。2、立銑刀和鑲硬質合金刀片的端銑刀主要用於切削凸台、凹槽和箱口面。
3、球刀、圓刀(亦稱圓鼻刀)常用於切削曲面和變斜角輪廓外形。而球刀多用於半精切削和精切削。鑲硬質合金鎢鋼銑刀的圓刀多用於開粗。
八、切削程序單有什麼作用?在切削程序單中應包括什麼內容?
1、切削程序單是數控切削工藝設計的內容之一,也是需要操作者遵守、執行的規程,是切削程序的具體說明,目的是讓操作者明確程序的內容、裝夾和定位方式、各個切削程序所選用的鎢鋼銑刀既應注意的問題等。2、在切削程序單里,應包括:繪圖和編程文件名,工件名稱,裝夾草圖,程序名,每個程序所使用的鎢鋼銑刀、切削的最大深度,切削性質(如粗切削還是精切削),理論切削時間等。
九、數控編程前要做何準備?
在確定切削工藝後,編程前要了解:1、工件裝夾方式;
2、工件毛胚的大小----以便確定切削的範圍或是否需要多次裝夾;
3、工件的材料----以便選擇切削所使用何種鎢鋼銑刀;
4、庫存的鎢鋼銑刀有哪些----避免在切削時因無此鎢鋼銑刀要修改程序,若一定要用到此鎢鋼銑刀,則可以提前準備。
十、在編程中安全高度的設定有什麼原則?
安全高度的設定原則:一般高過島嶼的最高面。或者將編程零點設在最高面,這樣也可以最大限度避免撞刀的危險。
十一、鎢鋼銑刀路徑編出來之後,為什麼還要進行後處理?
因為不同的工具機所能認到的地址碼和NC程序格式不同,所以要針對所使用的工具機選擇正確的後處理格式才能保證編出來的程序可以運行。
十二、什麼是DNC通訊?
程序輸送的方式可分為CNC和DNC兩種,CNC是指程序通過媒體介質(如軟盤,讀帶機,通訊線等)輸送到工具機的存儲器存儲起來,切削時從存儲器里調出程序來進行切削。由於存儲器的容量受大小的限制,所以當程序大的時候可採用DNC方式進行切削,由於DNC切削時工具機直接從控制電腦讀取程序(也即是邊送邊做),所以不受存儲器的容量受大小的限制。1、切削用量有三大要素:切削深度,主軸轉速和進給速度.切削用量的選擇總體原則是:少切削,快進給(即切削深度小,進給速度快)。
2、按材料分類,鎢鋼銑刀一般分為普通硬質白鋼刀(材料為高速鋼),塗層鎢鋼銑刀(如鍍鈦等),合金鎢鋼銑刀(如鎢鋼,氮化硼鎢鋼銑刀等)。