不同類型的仿形銑削對立銑刀表面粗糙度和刀具壽命的影響
2020-06-04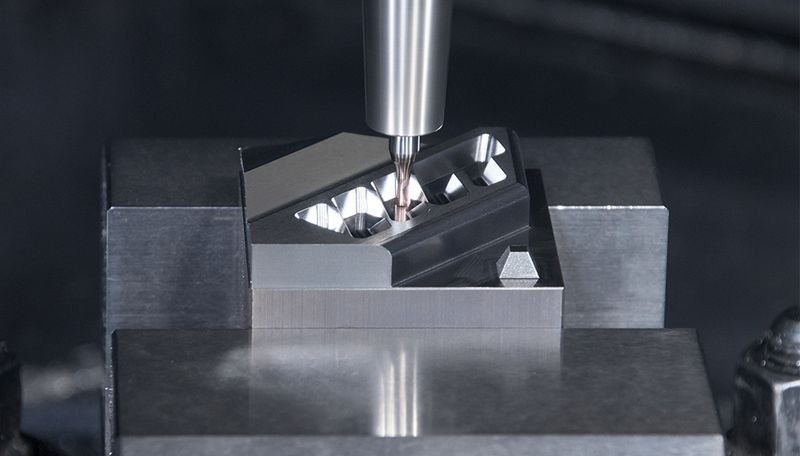
摘要
文章論述了球頭端銑刀的刀具壽命取決於上仿形和下仿形銑削的情況。目的是測定和比較不同類型的球頭立銑刀在不同刀具材料的仿形銑削加工中的磨損情況。此外,還測量和比較了上仿形和下仿形銑削時的表面粗糙度。此外,我們還研究和觀察了球頭端銑刀與被加工材料的刀具接觸面積。磨損試驗,採用DMG DMU 85單板數控五軸銑床進行磨損試驗。實驗中,一方面改變了刀具材料,另一方面改變了切削速度、進給速度、軸向切削深度和徑向切削深度。硬質合金和高速鋼作為刀具材料進行了試驗。刀具磨損是在Zoller Genius 3s通用測量機上測量的。採用Surtronic 3+(Taylor Hobson)進行表面粗糙度測量。結果表明,根據不同刀具材料的仿形銑削策略,球頭立銑刀的表面粗糙度和刀具壽命不同。
1. 導言
仿形面銑的刀路往往是上銑和下銑相結合,需要在切削過程中進行大量不利的切入和切出。在自由曲面銑削過程中,模具可以向上或向下加工。刀具相對於被加工面的位置(傾角)對切削力有很大的影響。刀具與工作面之間的夾角直接影響到拱形銑床的主動切削刃的長度和位置,而主動切削刃的長度和位置又會對切削過程產生很大的影響。不正確的刀具位置可能導致切削力突然增加和/或刀尖溫度超過各自的臨界值。Schulz和Hock用不同傾角的球頭銑刀來研究刀具壽命和工件質量,他們得出結論:刀具傾角在10°~20°範圍內的下銑/反切代表了模具製造行業高速銑削的最佳加工策略。
Chen根據表面誤差,對球頭銑刀的刀具路徑進行了優化,刀具路徑是指刀具實際運動的偏差。要想加工出準確的三維曲面,刀具路徑是至關重要的。Toh收集了刀具路徑和方向對切削力、刀具壽命和表面質量的影響。刀具路徑方向決定了切屑接觸面積的大小,從刀具壽命的角度來看,傾角是最佳值。在自由曲面3D銑削的情況下,傾角是逐點變化的,但在5D銑削的情況下,傾角可以保持不變。在5軸數控機床上,刀具位置很容易進行修正,而5軸數控機床的購置和維護費用較高,因此攤銷費用較高。在加工過程中遇到的兩個關鍵問題是:刀具壽命短,難以提供所需的表面光潔度。Zetek等人觀察了Inconel 718的端面銑削過程中的側翼磨損,並測量了切削力。他們優化了刀刃半徑的尺寸,使刀具壽命提高了約20%。Kasim等人發現,在Inconel 718端面銑削過程中,缺口磨損是主要的失效模式。Begic-Hajdarevic等人研究了切削參數對上銑和下銑過程中表面粗糙度的影響。在最近的研究中,研究了硬質合金球頭立銑機的磨損測量過程。在這個實驗中,確定了上切削和下切削對球頭端銑刀表面粗糙度和刀具壽命的影響,並對不同刀具材料進行了比較。
2. 材料和實驗方法
2.1. 工件材料
所選工件材料為ISO C45(AISI 1045)級中碳鋼。化學成分和機械性能如表2和表3所示。工件材料的尺寸為100×100×60 mm。工件的模型在CAD系統中進行。
表1.加工材料的化學成分 機加工材料C45的化學成分

2.2. 經測試的切割工具
球頭端銑機(試樣)的應用是典型的模具銑削加工。它與球頭端銑刀在仿形銑中的運動學表示有關。測試的切削刀具材料為無塗層硬質合金(MicroGrain)和高速鋼(HSS-Co5)。
我們研究了四種版本。
•S1 - 硬質合金球頭立磨機,用於上仿形加工。
•S2 - 硬質合金球頭端銑削機,用於下仿形加工。
•S3 - HSS-Co5型球頭端銑床,用於上仿形加工。
•S4 - HSS-Co5球頭端銑床,用於下仿形加工。
我們研究了四種版本。
•S1 - 硬質合金球頭立磨機,用於上仿形加工。
•S2 - 硬質合金球頭端銑削機,用於下仿形加工。
•S3 - HSS-Co5型球頭端銑床,用於上仿形加工。
•S4 - HSS-Co5球頭端銑床,用於下仿形加工。
表2. WOTEK球銑刀的參數

2.3. 刀具壽命測試和表面粗糙度測量
仿形銑床採用DMG DMU 85 monoBLOCK五軸數控銑床(圖1a)。首先,在CAM系統中生成了數控機床的程序。在加工過程中沒有使用冷卻液。在切削試驗中,我們設定了相同的切削條件(切削速度、進給速度、軸向和徑向切削深度)。因此,我們打算在相同的切削參數下,只研究刀具平面上的刀具接觸面積對球頭端銑刀磨損的影響。工件的傾角為15°。Tonshoff等人發現,對於塊狀材料的球頭立銑,最佳傾角為15°。
由於球頭立銑刀的側翼磨損占主導地位,因此在Zoller Genius 3s萬能測量機上進行測量(圖1b)。每隔10.75分鐘測量一次,相當於2m的切削長度。當側面磨損達到0.3 mm以上和HSS-Co5銑刀的側面磨損達到0.2 mm以上時,停止了硬質合金銑刀的加工試驗。由於超過這個值就會出現邊緣崩解。此外,工件材料的表面粗糙度是在切削10.75 min後,當球頭端銑刀達到側向磨損標準(硬質合金銑刀為0.3 mm,高速鋼-Co5銑刀為0.2 mm)時,測量工件材料的表面粗糙度。 Surtronic 3+用於表面粗糙度測量。
%20workplace%20of%20DMG%20DMU%2085%20MonoBLOCK%3B%20(b)%20measuring%20of%20flank%20wear%20on%20Zoller%20Genius%203s.jpg)
由於球頭立銑刀的側翼磨損占主導地位,因此在Zoller Genius 3s萬能測量機上進行測量(圖1b)。每隔10.75分鐘測量一次,相當於2m的切削長度。當側面磨損達到0.3 mm以上和HSS-Co5銑刀的側面磨損達到0.2 mm以上時,停止了硬質合金銑刀的加工試驗。由於超過這個值就會出現邊緣崩解。此外,工件材料的表面粗糙度是在切削10.75 min後,當球頭端銑刀達到側向磨損標準(硬質合金銑刀為0.3 mm,高速鋼-Co5銑刀為0.2 mm)時,測量工件材料的表面粗糙度。 Surtronic 3+用於表面粗糙度測量。
%20workplace%20of%20DMG%20DMU%2085%20MonoBLOCK%3B%20(b)%20measuring%20of%20flank%20wear%20on%20Zoller%20Genius%203s.jpg)
圖1.DMG DMU 85 MonoBLOCK的加工場所。(a) DMG DMU 85 MonoBLOCK的工作場所;(b)測量Zoller Genius 3s的側面磨損
2.4. 切削條件所有刀具壽命試驗均採用以下參數進行:
切削速度vc=70 m/min,主軸轉速n=1856.8 1/min,進給速度vf=186 mm/min,軸向切削深度ap=0.5 mm ,徑向切削深度ae=0.5 mm,每齒進給量fz=0.05 mm。
2.5. 在仿形銑削中的有效切削半徑和有效切削速度
在上仿形銑削時,切向曲線位於球頭銑刀的旋轉軸線的一側。在下仿形銑削時,切線曲線是以球頭端銑床的旋轉軸線為中心,從球頭端銑床的旋轉軸線的兩側穿過球頭端銑床的旋轉中心。仿形銑削的標示方案如圖2所示。
%20Scheme%20of%20up-copying%3B%20(b)%20scheme%20of%20down-copying.jpg)
%20Scheme%20of%20up-copying%3B%20(b)%20scheme%20of%20down-copying.jpg)
圖2. (a) 向上仿形銑削方案;(b) 向下仿形銑削方案
圖2中的符號
R - 刀具半徑(mm)
ap - 切削深度(mm)
VF - 進料率(mm/min)
ap,max - 最大切削深度(mm)
α- 銑削面坡度角(°)
ap,iden - 相同的切削深度(mm)
n - 主軸轉速 (1/min)
ap,crit- 臨界深度(mm)
Ref1 - 刀具的有效半徑
Ref2 - 刀具在加工表面上的有效半徑(mm) 在工作面上的有效半徑(mm)
有效半徑的確定對於獲得有效切削速度是非常重要的。有效半徑和有效切削速度的計算公式有以下幾種形式。
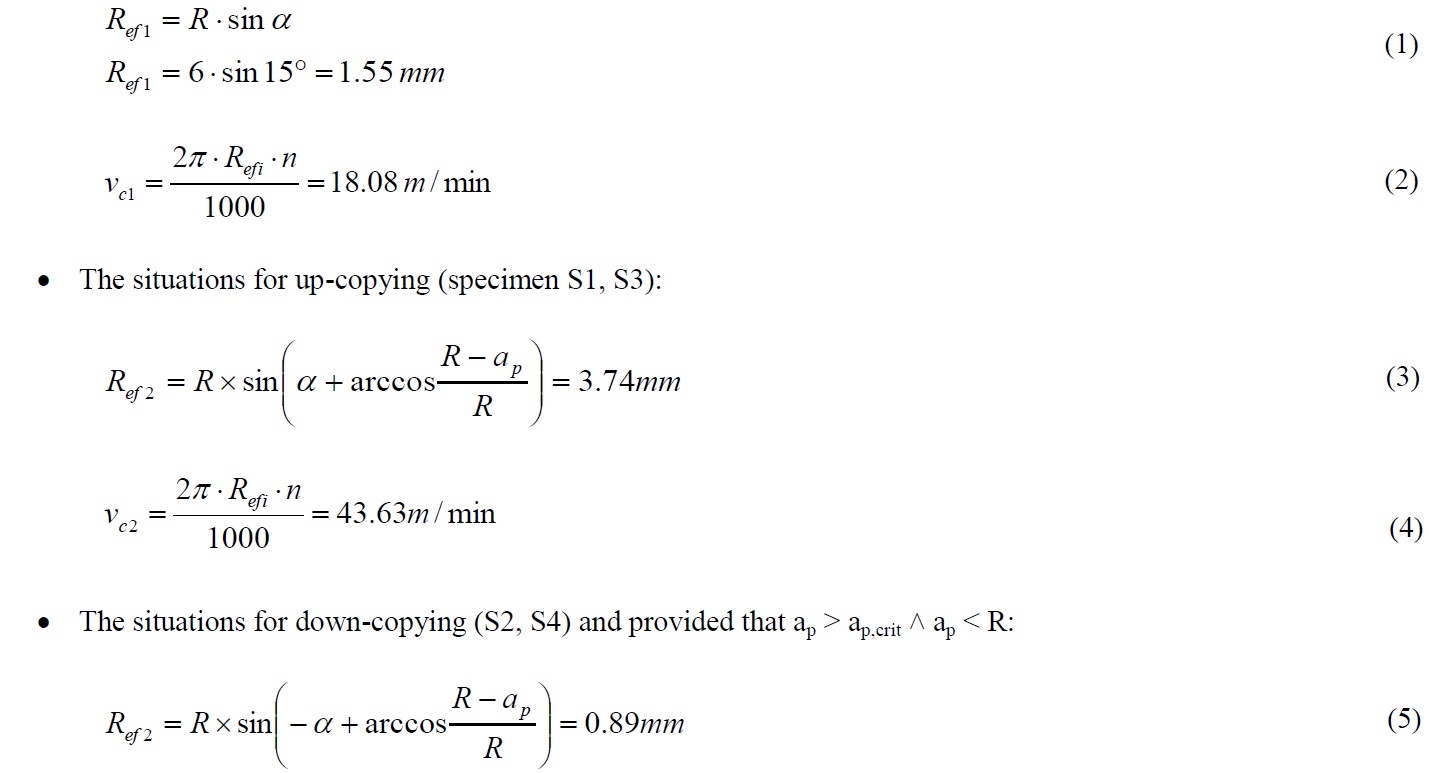
從有效切削速度的方程計算結果來看,有效半徑Ref1和Ref2中的較大者的切削速度最高。因此,在向上仿形銑削(公式3),Ref2>Ref1時,有效切削速度為Ref2(公式4)。由於在向下仿形銑削時(公式5),Ref2 < Ref1,因此,有效切削速度計算為Ref1(公式2)。
ap - 切削深度(mm)
VF - 進料率(mm/min)
ap,max - 最大切削深度(mm)
α- 銑削面坡度角(°)
ap,iden - 相同的切削深度(mm)
n - 主軸轉速 (1/min)
ap,crit- 臨界深度(mm)
Ref1 - 刀具的有效半徑
Ref2 - 刀具在加工表面上的有效半徑(mm) 在工作面上的有效半徑(mm)
有效半徑的確定對於獲得有效切削速度是非常重要的。有效半徑和有效切削速度的計算公式有以下幾種形式。
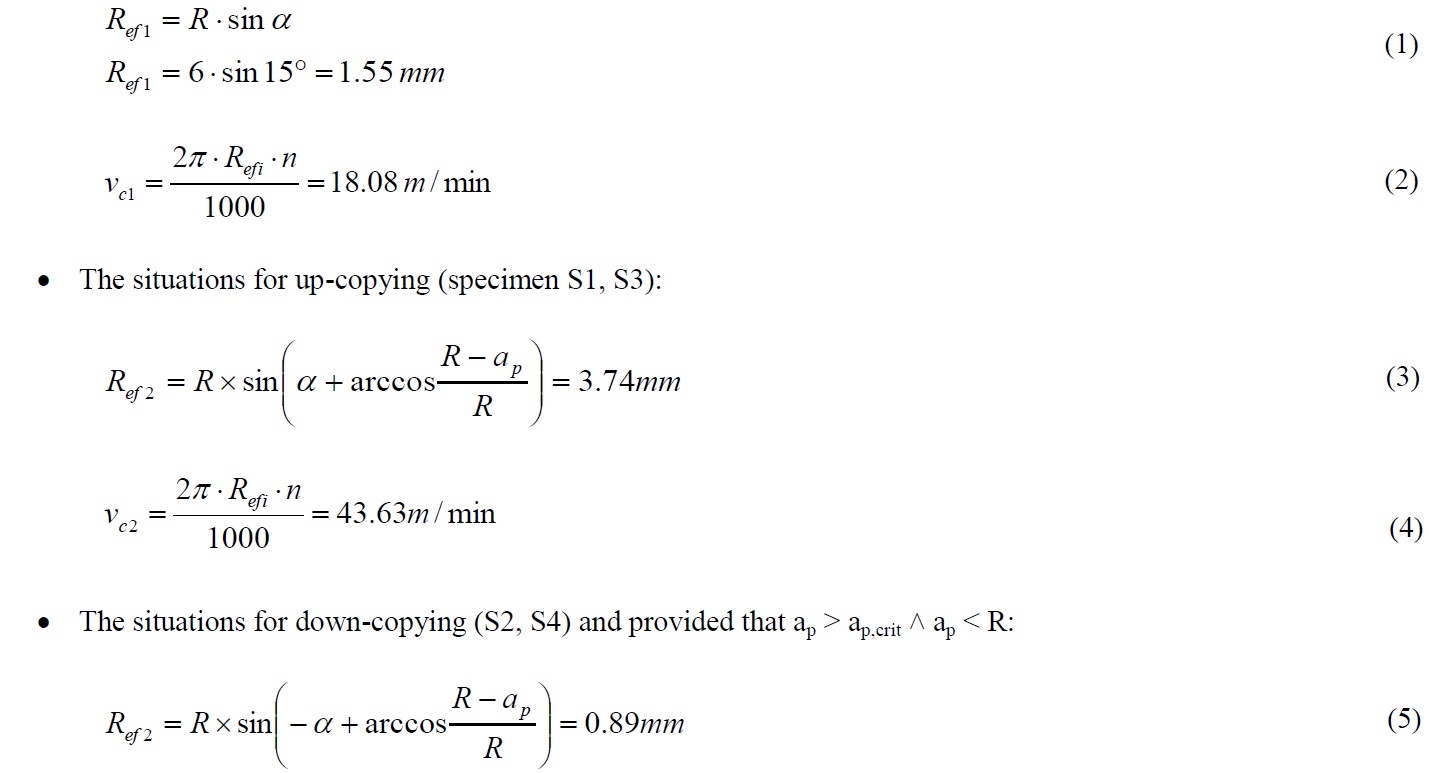
從有效切削速度的方程計算結果來看,有效半徑Ref1和Ref2中的較大者的切削速度最高。因此,在向上仿形銑削(公式3),Ref2>Ref1時,有效切削速度為Ref2(公式4)。由於在向下仿形銑削時(公式5),Ref2 < Ref1,因此,有效切削速度計算為Ref1(公式2)。
3. 結果
3.1. 顯微照片中測量到的側面磨損情況
圖3和圖4所示為硬質合金球頭端銑刀的側面磨損實測圖。圖3為硬質合金球頭端面銑刀側面的顯微圖,圖4為高速鋼-Co5球頭和銑刀側面的顯微圖。前兩列為上銑時的側翼磨損顯微圖。另兩列為下銑時的側翼磨損顯微圖。圖3a和圖4a記錄了球鼻端銑刀在切削前0min的時間內的磨損情況。此外,圖3b和圖4b分別為硬質合金銑刀和高速鋼-Co5銑刀達到0.3mm以上和0.2mm以上後的側面磨損。圖5),在這些值之上,觀察到了邊緣磨損的情況。
%20carbide%20ball%20nose%20end%20mill%20before%20cutting%2C%20(b)%20flank%20wear%20after%20attaining%20the%20value%20of%200_3%20mm.png)
%20carbide%20ball%20nose%20end%20mill%20before%20cutting%2C%20(b)%20flank%20wear%20after%20attaining%20the%20value%20of%200_3%20mm.png)
圖3. (a)切削前的硬質合金球頭端銑刀,(b)達到0.3 mm值後的側翼磨損情況
%20HSS-Co5%20ball%20nose%20end%20mill%20before%20cutting%2C%20(b)%20flank%20wear%20after%20attaining%20the%20value%20of%200_2%20mm.jpg)
圖4. (a)切削前的HSS-Co5球頭端銑刀,(b)達到0.2mm值後的側翼磨損情況
%20edge%20chipping%20of%20carbide%20mill%20for%20up-copying%2C%20(b)%20edge%20chipping%20of%20HSS-Co5%20mill%20for%20down-copying.jpg)
圖5. (a)用於上仿形銑削的硬質合金銑刀,(b)用於下仿形銑削的高速鋼-Co5銑刀
3.2 刀具壽命測試的評價
磨損測量過程的下一步是對刀具壽命測試的評價。首先,在銑削前開始對Zoller Genius 3S的測量系統進行校準。對第一刀刃和第二刀刃進行了特定的磨損測量。確定了平均值,並將其插入表3中。
試樣S1、S2、S3和S4的側面磨損值見表3和表4。S1的側面磨損值在切削64.5min後達到了0.3mm以上。從第7號的測量結果可以看出,第2個齒的側面磨損值與第6號的側面磨損值相同。這是由於邊緣崩解造成的。齒側磨損增加,但由於切削刃的崩解,導致齒側磨損的測量值下降。對於S2,在切削86min後,側翼磨損值達到了0.3mm以上。對於S3,32.25 min後,側面磨損值達到0.2 mm以上,對於S4,43 min後,側面磨損值達到0.2 mm以上。
試樣S1、S2、S3和S4的側面磨損值見表3和表4。S1的側面磨損值在切削64.5min後達到了0.3mm以上。從第7號的測量結果可以看出,第2個齒的側面磨損值與第6號的側面磨損值相同。這是由於邊緣崩解造成的。齒側磨損增加,但由於切削刃的崩解,導致齒側磨損的測量值下降。對於S2,在切削86min後,側翼磨損值達到了0.3mm以上。對於S3,32.25 min後,側面磨損值達到0.2 mm以上,對於S4,43 min後,側面磨損值達到0.2 mm以上。
表3. 不同類型仿形銑刀的硬質合金球頭端面銑刀的側面磨損值
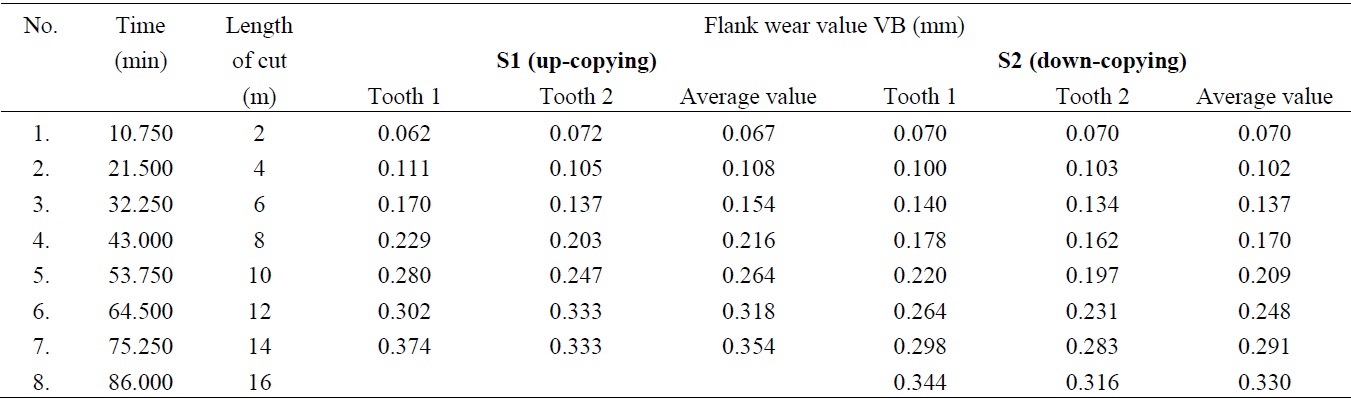
表4. HSS-Co5球頭端面銑刀在不同類型仿形銑削時的側面磨損值
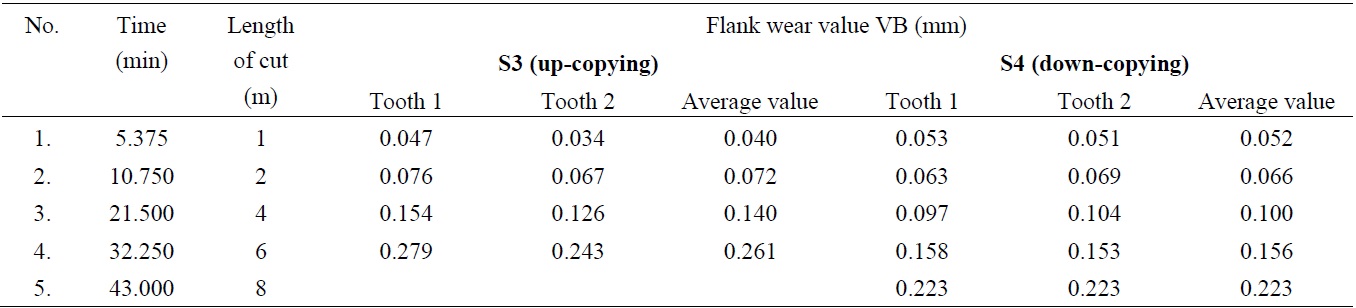
圖6中的圖表是基於特定測量值的側翼磨損值繪製的圖,表示了側翼磨損的時間依賴性。然後比較了試樣S1、S2、S3和S4的側面磨損的時間依賴性。
從圖中可以看出,下銑的刀具壽命比上銑的刀具壽命長。對於硬質合金銑刀,S2的刀具壽命比S1長40%。對於高速鋼-Co5銑刀,S4的刀具壽命比S3長50%。我們假設這是由於2.5章中提到的各種有效弧度造成的。因此,有效切削速度隨有效半徑的不同而改變。在向上仿形銑削時的有效切削速度是向下仿形銑削時的2.41倍。從泰勒方程中可以看出切削速度的重要性,因為該公式只依靠切削速度來估算刀具壽命。方程6也叫泰勒刀具壽命方程式。從這個方程式中可以得出,切削速度的增加會導致刀具壽命的降低。由此可知,由於有效切削速度較低,在下式仿形銑削中,刀具壽命比上式仿形銑削中的刀具壽命長。

其中: VC - 切割速度(m/min)
Vc - 切削速度(m/min)
Tc1/k - 泰勒指數
C - 常數。
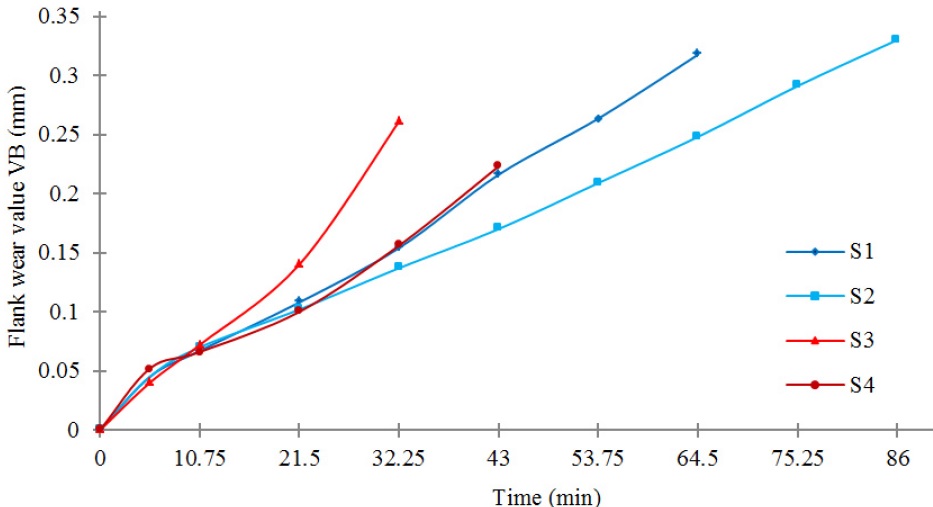
圖6. 側翼磨損的時間依賴性
3.3. 表面粗糙度測量的評價
球頭端面銑床(S1、S2、S3和S4)工件材料表面粗糙度的測量比較如圖7所示。每次測量均進行了5次。粗糙度測量結果表明,上銑時的Ra優於下銑時的粗糙度。
經過10.75分鐘的切削,測得的平均粗糙度(Ra)為
•上仿形銑削時:對於硬質合金銑刀(S1),Ra=1.16μm;對於高速鋼-Co5銑刀(S3),Ra=1.54μm。
•下仿形銑削加工:對於硬質合金銑刀(S2),Ra=1.58μm,對於高速鋼-Co5銑刀(S4),Ra=2.41μm
•下仿形銑削加工:對於硬質合金銑刀(S2),Ra=1.58μm,對於高速鋼-Co5銑刀(S4),Ra=2.41μm
在達到側翼磨損標准後,平均粗糙度(Ra)為
•上仿形銑削:對於硬質合金銑刀(S1),Ra=1.69μm,對於高速鋼-Co5銑刀(S3),Ra=2.07 μm。
•下仿形銑削加工:對於硬質合金銑刀(S2),Ra = 2.02μm,對於高速鋼-Co5銑刀(S4),Ra = 3.42μm
•下仿形銑削加工:對於硬質合金銑刀(S2),Ra = 2.02μm,對於高速鋼-Co5銑刀(S4),Ra = 3.42μm
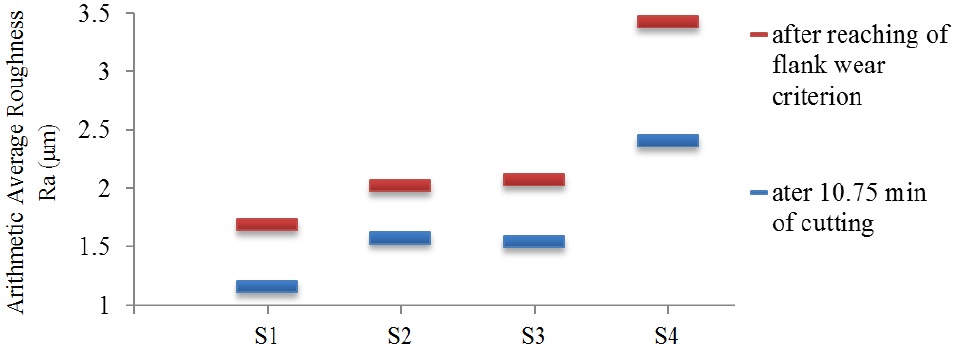
圖7.上仿形銑削和下仿形銑削時的表面粗糙度
結論
目的是確定不同類型的仿形銑削對立銑刀表面粗糙度和刀具壽命的影響。刀具磨損的標準是側面磨損,因為它是主要的磨損。我們研究了兩種刀具材料(硬質合金和高速鋼-Co5),四種切削刀具(試樣S1、S2、S3和S4),並設定了相同的切削條件。首先計算出球頭端銑刀的磨損刀具接觸面積,然後在Zoller Genius 3s萬能測量儀上觀察。刀具壽命測試,採用DMG DMU 85單板數控五軸銑床。
研究結果顯示,不同類型的仿形銑削樣品的刀具壽命不同。其中,向下仿形銑削樣品的刀具壽命比向上仿形銑削的刀具壽命長。對於硬質合金銑刀,S2的刀具壽命比S1長40%,而對於高速鋼-Co5銑刀,S4的刀具壽命比S3長50%。我們認為,由於在仿形銑削過程中有效切削速度較低,所以在向下仿形銑削中的刀具壽命比向上仿形銑削中的刀具壽命長。
因此,當刀具壽命是主要的考量時,選擇下銑加工時是最好的方法。另一方面,在上銑加工中的切削刀具顯示出較低的Ra值。未來的研究將通過修磨和研磨銑刀為參考。本研究將以刃口處理對球頭立銑刀在模具銑削中的刀具壽命的影響為研究方向。
研究結果顯示,不同類型的仿形銑削樣品的刀具壽命不同。其中,向下仿形銑削樣品的刀具壽命比向上仿形銑削的刀具壽命長。對於硬質合金銑刀,S2的刀具壽命比S1長40%,而對於高速鋼-Co5銑刀,S4的刀具壽命比S3長50%。我們認為,由於在仿形銑削過程中有效切削速度較低,所以在向下仿形銑削中的刀具壽命比向上仿形銑削中的刀具壽命長。
因此,當刀具壽命是主要的考量時,選擇下銑加工時是最好的方法。另一方面,在上銑加工中的切削刀具顯示出較低的Ra值。未來的研究將通過修磨和研磨銑刀為參考。本研究將以刃口處理對球頭立銑刀在模具銑削中的刀具壽命的影響為研究方向。
致謝
這項貢獻是斯洛伐克共和國教育、科學、研究和體育部GA VEGA項目的一部分,項目編號:1/0615/12 "五軸磨削參數對刀柄刀具幾何精度的影響"。這一貢獻還得到了歐洲區域發展基金共同資助的五軸加工高級研究與發展中心業務項目ITMS 26220120013的支持。